Creation
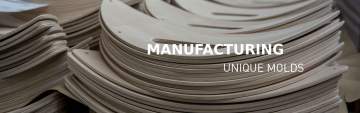
MANUFACTURING SEATS
We design shells, curves and unique seating that enhance professional spaces for various trades:
Architects / Designers / Fitters / Restaurateurs / Communities / Companies
Create your custom product:
Shells: plywood pieces comprising a backrest and seat in a 3D curve, bringing comfort and design to the chair.
Seats: these have a round or U-shaped bowl, with or without a flap.
Backrests: these have a straight part that fits into two studs or are very curved for excellent lumbar support.
Radiuses:: numerous moulds with a bending radius between 160 and 4,500mm.
Our various areas of expertise:
Peeling / Pressing / Machining / Sanding / Surface treatments / Finishing
Our design office supports your projects, from creation to mass production and high volumes, according to your needs.
Mission
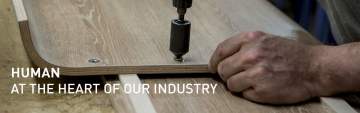
QUALITY & HERITAGE
Our expertise in moulded wood stems from our unique wood processing method, which has been handed down for more than 50 years.
Since 1949, we have been continuing to strive to improve our expertise through the use of the best technologies: CNC machines, automated production lines and state-of-the-art robotics.
Today, the special partnerships we have developed over the years enable us to work with peeled wood.
Our industrial expertise is a result of our capacity to innovate continuously and think today about the moulded plywood industry of tomorrow.
Principles
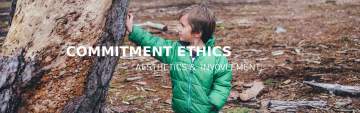
HIGH STANDARDS, ETHICS, AESTHETICS & COMMITMENT
- Demand for high level work and high quality seats, with an original crafted curve.
- Team ethics and professionalism, elegance and performance in business.
- Aesthetics in the development of our products, through inspiration from other creative worlds and areas such as art, design, photography and fashion.
- Commitment to corporate and social responsibility, the environment (R&D in recycling) and education (we provide support to children from all walks of life, to help them succeed in their future).
Responsible approach
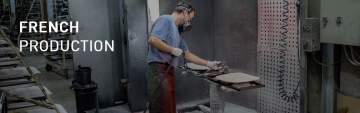
FRENCH PRODUCTION
French supply
Our veneers and plywoods come predominantly from France, mainly from the Bourgogne, Franche Comté and Grand Est regions.
The quality
We constantly improve our processes and wish to be retroactive in terms of Quality, from the documentation in the production.
Fire classification
We study every requests according to the levels of classification to be reached.
Certifications
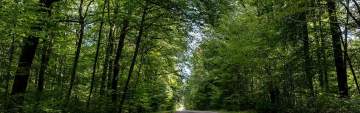
FOREST MANAGEMENT
PEFC certification, Régnier’s commitment to sustainable forest management
Régnier’s four steps to ensuring the sustainable management of forest resources:
- Forestry and wood harvesting
- Wood material tracking
- Wood processing
- End product marketing
Regnier Factory

CLOSEST TO YOUR NEEDS
- 12,000 sqm of production sites in Champagne
- 3 Ha of sites
- + 100 employees
- 57 presses
- 6 robots
- + 2 million pieces / year
- 65% of sales turnover on export
- 150 molds
- + 5 wood species
- 17 colors
- 11 wood combination colors
- 12 types of sliced veneer